A Conversation with a chair, two ladders and a passer-by
Field notes written with Gary Edwards presented at the Acadia 2020 Conference ‘Distributes Promiximities’
about the robotically fabricated prototypes for
Monitor with Greg Storrar and sculptor James Capper.
Research Assistants: Gary Edwards, Cristina Garza, Theo Tan
Someone walking past the robotics lab, seeing the steel panel with the shape of a chair pressed into it, asks us how we have managed to vacuum-form steel. ... continue reading below ...
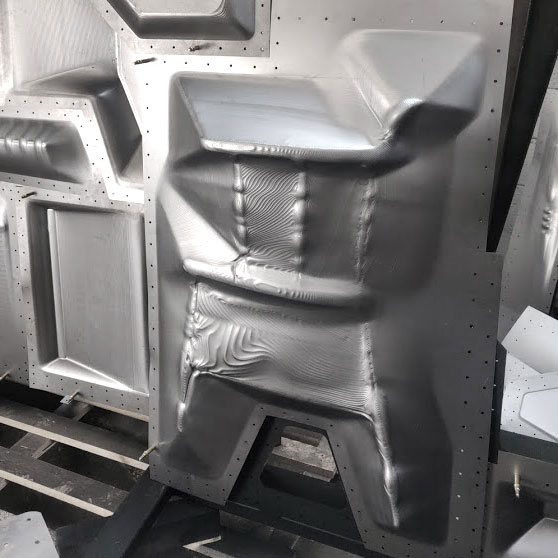

The chair belongs to James, we explain, the sculptor with whom we are designing and building a mobile artist studio. James has become famous for making fantastically absurd sculptures – he is just finishing a boat that will pull itself up the bank of the Thames, inspired by the comical amphibian mudskipper after which it is named. Like all of James’ sculptures, it actually works.
Now we are collaborating on the next amphibious sculpture inspired by lizard locomotion. The chair is one of many objects that will come on its expeditions and will be stowed away into the wall of the extremely compact studio. We picked the old-fashioned piece, with its leather upholstering, turned legs and backrest stiles because it conjures up images of Admiral Nelson´s chair on the HMS Victory – only that now, in an odd hybridisation of pre-industrial and post-industrial manufacturing processes, it is 3D-scanned and robotically formed.
Video by Greg Storrar
All of the 50+ panels of the 1:1 prototype wall that we are currently building are fabricated using robotic Single Point Incremental Forming (SPIF). But it is whilst prototyping this chair panel, with its awkward geometry and challenging depth, that we tear the most sheets, blunt the most end effectors – and consequently learn the most. We learn that the flexible timber framework backing the panels, which we developed because it was quick, cheap and variable, had the added advantage of yielding to forces, which compensates for the more unforgiving material constraints of the sheet steel we are forming. We learn that, as the robot gradually presses the panel into shape, the timber sub-structure tends to creak like an old sailing boat. We learn that our end effector should equally be softer than the material it is forming and finally settle on a brass stylus, which we have to sharpen like a pencil between forming. 



Because the chair is difficult (and perhaps slightly silly), because it tells the fabrication process what to do rather than just listening to what it has on offer, we learn how to analyse and optimise formable geometries: filtering the scan according to draft angles; smoothing and relaxing the mesh; modelling the surface between the scan and the edge of the formable surface according to allowable geometrical constraints (many quantifiable, many intuited) for robotic forming. We learn to generate toolpaths that minimise the common SPIF ‘pillow effect’ and continue to battle what we call the ‘pinching effect’, an extreme case of pillowing that appears specifically at the point where the long valleys around the chair’s legs close in on themselves and accumulate (or ‘pinch’) excess material.
Our dialogue with the chair, or rather the dialogue between the chair and the sheet with us as mediators, becomes more interesting when more voices join in. A conversation between the studio’s two skins unfolds. The exterior 0.9mm steel skin is riveted onto a structural frame (the very same frame we use for forming, with a set of standardised clamping plates, to secure the blank panels in the first place) whereas the interior 0.9mm aluminium skin is hung, thermally separated, from the load-bearing exterior frame.
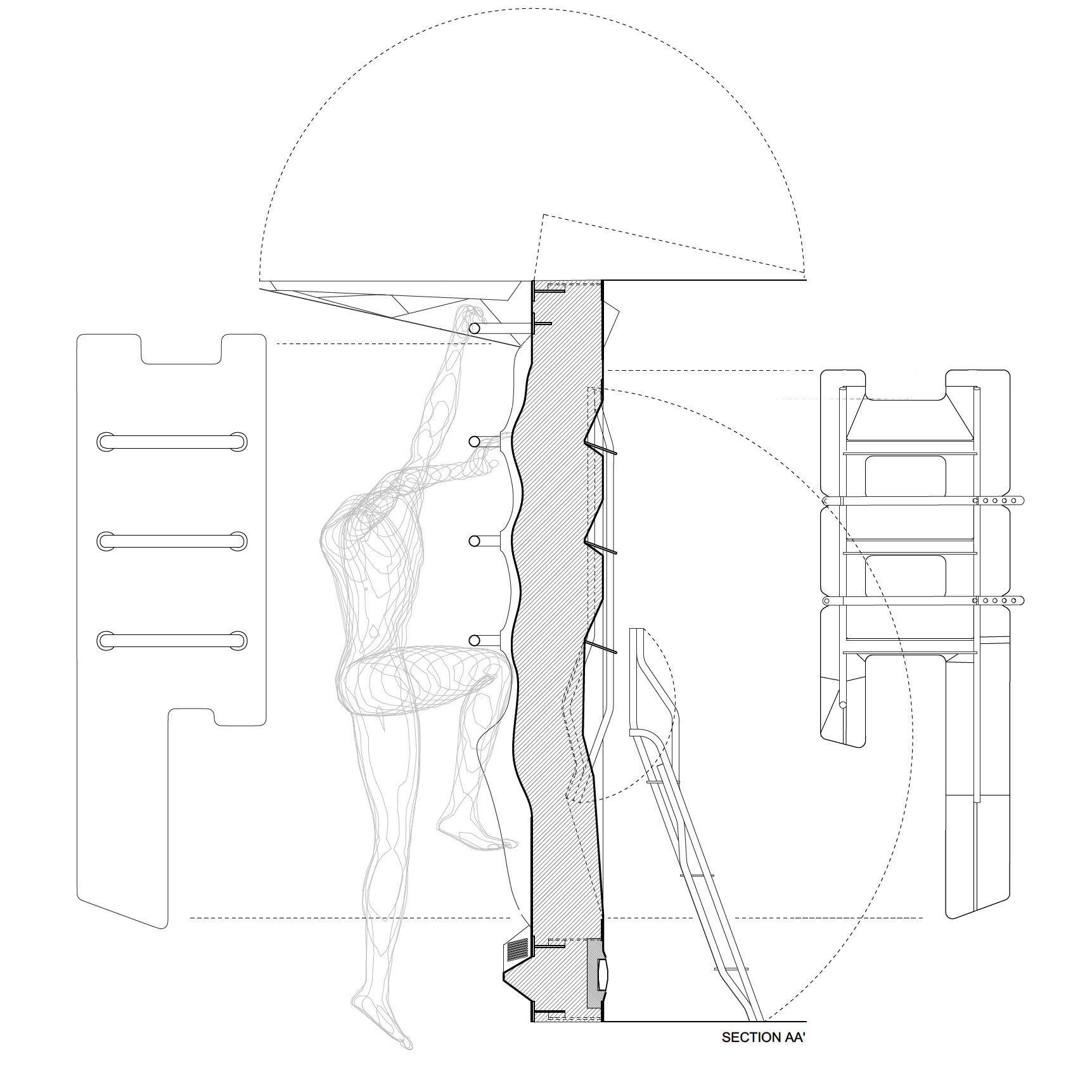


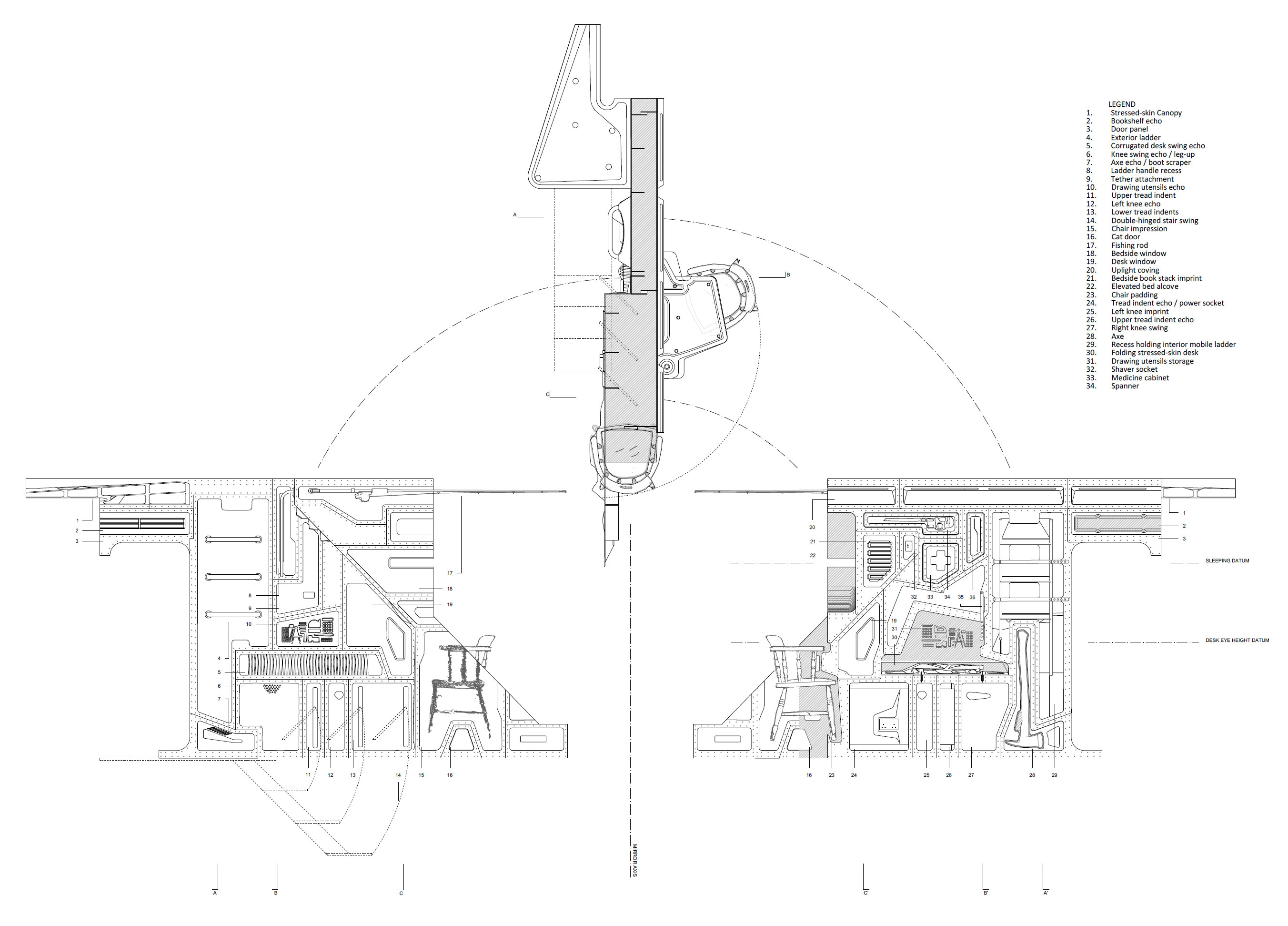
The conversation between the two skins is marked by transformations and productive mistranslations: an axe head inside offers a boot scraper outside; the swing of James’ knee, sitting at his desk on the inside, presses into the aluminium skin, the knee cap traced by a secondary toolpath expressing the patella structure, and translates as a bulge on the outside, where it is used as a leg-up to climb an exterior ladder and access the studio’s roof. A secondary dotted pattern, added to the upper leg, provides extra grip to this step. The inner sitter helps the outer climber.

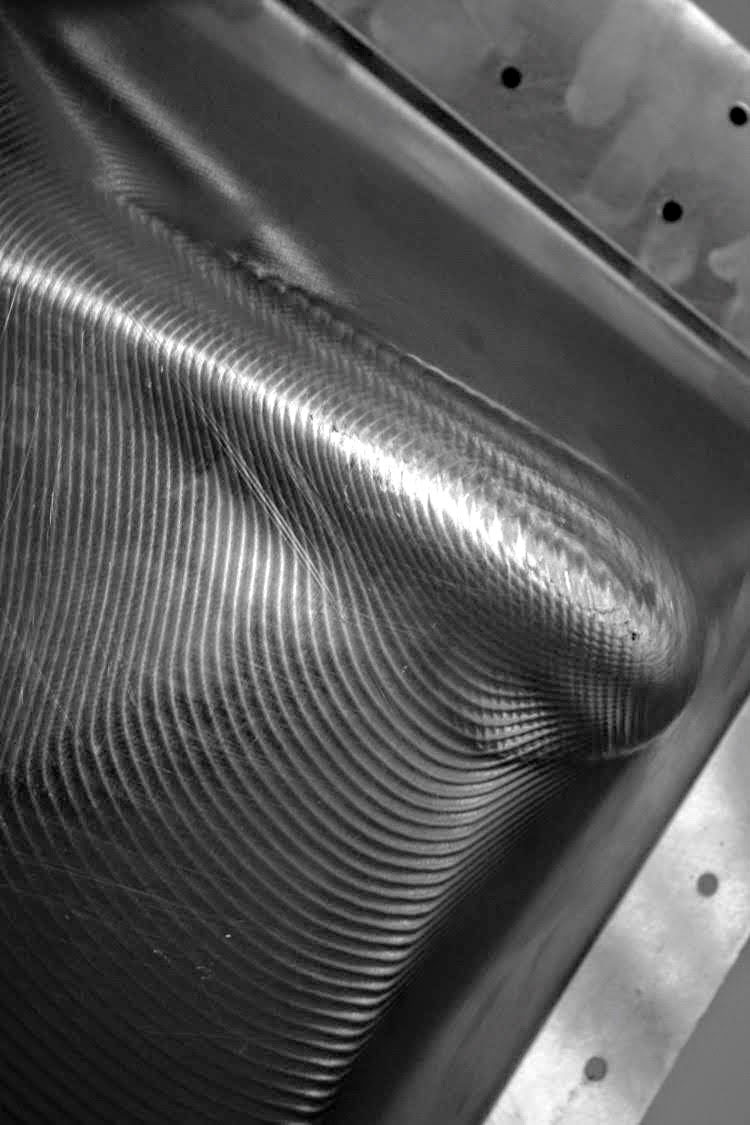
Without touching, through the mediation of the thick in-between of the physical wall, of the digital modelling process and the material and robotic fabrication constraints, the two skins modulate each-other, resulting in strange hybrids. The exterior ladder, for example, echoes a moveable ladder on the inside, transforming the intersection of its treads and stringers to form three pairs of circular protrusions, ‘nipples’ that accept the bent rungs for the exterior ladder. Below these nipples, another knee emerges, which, rather than an echo of an internal knee, follows the need for an additional step between the first knee and the first rung. The ladder’s knee is the deepest and steepest piece of forming we do.

We have nearly forgotten the person who had prompted our train of thought with the initial question about the chair panel – and who is still listening, though seeming slightly puzzled about how the conversation has moved from a timber chair to walls growing nipples and ladders begetting knees. Perhaps the project’s conceptual framework has escalated? But then again, perhaps by doing so, it has continued to challenge us as digital makers? And perhaps, within the cross-contamination between bodies, objects, skins and code, another type of knowledge has emerged – a hybrid knowledge? In the background, the creaking boat sound grows louder and louder, it is time we sharpen our brass pencil.
Acknowledgements
Monitor, the mobile studio discussed in this piece, is a project by James Capper, Thomas Pearce and Greg Storrar.
The team at The Bartlett School of Architecture (University College London): Thomas Pearce, project lead, design; Greg Storrar (ARB) design; Gary Edwards (ARB), robotics; Theo Tan and Cristina Garza Lasierra, research assistants.
This project is made possible thanks to generous support from the Higher Education Innovation Fund (UCL Knowledge Exchange grant), the Bartlett’s Architectural Project Fund, Hannah Barry Gallery (London), Izolyatsia (Kyiv) and Tata Steel. Many thanks to the staff at B-Made for enabling and supporting our research. The robotic incremental sheet forming in this project was initially based on a research project developed by Cristina Garza (DfM) in collaboration with Vincent Huyghe of B-Made.